What Is Fretting Fix in Automotive?
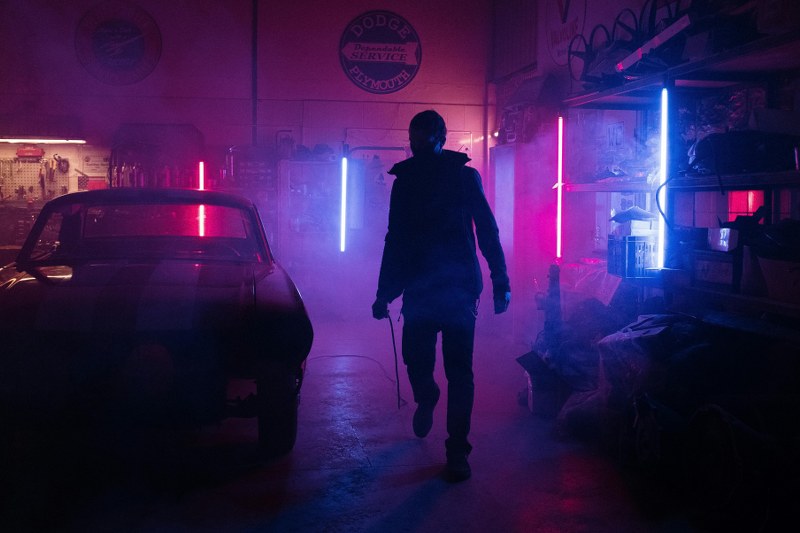
What Is Fretting Fix in Automotive? Overview: Fretting is a significant yet often overlooked issue in automotive design and maintenance, causing wear and corrosion in various components due to small, repeated movements. This phenomenon, particularly prevalent in automotive applications, can affect vehicles’ performance, reliability, and longevity, making understanding and addressing fretting essential for vehicle maintenance and component design.
In this article, we’ll explore fretting, how it manifests in automotive systems, its impact on various components, and the best solutions and fixes to mitigate fretting damage.
Understanding What Is Fretting Fix in Automotive Systems:
Fretting is the damage caused by repeated small amplitude oscillatory motion between two mating surfaces. These surfaces may experience micro-sliding or vibrations under pressure, resulting in the wear and degradation of the materials in contact.
Although the movements are often microscopic—typically ranging from micrometers to millimeters—this repeated motion can still cause significant damage over time, especially in high-stress automotive environments.
In an automotive context, fretting is common in several areas, including electrical connectors, joints, bearings, and fasteners, where parts are subject to vibrations and small relative movements. While the damage may seem minor initially, it can accumulate, leading to failure, malfunction, or reduced performance of key systems.
The Key Forms of Fretting in Automotive Systems
Fretting in automotive applications is primarily categorized into three types of wear damage:
- Fretting Wear: This form of fretting occurs when material is lost from the surface of the contact area due to the repeated rubbing motion. It can cause surface roughness, scratches, and microscopic pits, reducing the structural integrity of the parts involved. This wear can significantly affect functionality in automotive components such as engine parts and fasteners.
- Fretting Corrosion: Fretting corrosion occurs when the wear debris generated by fretting undergoes chemical reactions, particularly oxidation. This is especially problematic in electrical connectors, where the buildup of oxide layers can cause poor electrical contact, leading to power losses, signal degradation, or even complete system failure.
- Fretting Fatigue: Fretting fatigue involves the weakening of the material due to the repeated stresses from oscillatory motion. This can lead to cracking, material failure, and eventual component breakdown, which may not be immediately visible but could have catastrophic effects over time.
Common Automotive Components Affected by Fretting
Several automotive systems are prone to fretting due to their inherent design and operational environments. These components include:
- Electrical Connectors: As mentioned earlier, vehicle connectors are particularly vulnerable to fretting. This happens due to the vibrations caused by the engine and road conditions, which can lead to micro-movements between the connector terminals. Over time, this can wear down the connector’s surface coating and lead to oxidation, increasing resistance and potentially causing power or signal loss.
- Suspension Joints and Fasteners: Suspension components are subject to continuous stress and movement, and the small oscillations in these joints can lead to fretting damage. This can degrade the performance of the suspension system, affecting ride quality and handling.
- Engine Mounts and Bearings: Engine mounts, designed to absorb vibrations, are particularly susceptible to fretting due to their constant motion under engine load. Fretting in bearings, whether in the engine, transmission, or other moving parts, can cause premature failure, leading to expensive repairs or even complete breakdowns.
- Brake Systems: Braking components, such as pads, rotors, and calipers, are constantly subjected to mechanical forces and friction. Over time, fretting can cause wear and degradation of these parts, reducing braking efficiency and safety.
- Transmission Components: In automatic and manual transmissions, various components are in constant motion and are susceptible to fretting. This includes shafts, gears, and seals, which can experience micro-sliding due to the high vibrations and forces involved in the vehicle’s operation.
Signs of Fretting in Automotive Systems:
Detecting fretting damage early is essential for preventing more severe issues in the future. Some common signs of fretting in automotive components include:
- Increased Resistance in Electrical Systems: In connectors, the buildup of oxide layers can lead to higher resistance, manifesting as electrical issues, such as intermittent power or signal failures. This is often noticed as faulty dashboard lights, malfunctions in electrical systems, or poor performance of electrical devices.
- Abnormal Wear or Surface Degradation: In mechanical parts, fretting can cause visible signs of wear, including scratches, grooves, or pitting on the surface of the components. These signs of wear are often more pronounced in areas with high contact pressure and movement.
- Noise and Vibration: Components suffering from fretting wear or fatigue may produce unusual noises or vibrations, such as rattling sounds in the suspension or transmission. These noises indicate that the components no longer function optimally due to material degradation.
- Decreased Performance: A reduction in the performance of specific systems, such as suspension, transmission, or electrical systems, can indicate that fretting has caused internal damage to critical parts.
Preventing and Fixing Fretting in Automotive Systems:
Fretting damage can be costly and damaging to a vehicle’s overall performance, so prevention and mitigation strategies are crucial. Here are some of the most effective ways to fix and prevent fretting in automotive applications:
1. Material Selection and Coatings
Choosing the right materials for automotive components is one of the most effective ways to mitigate fretting. Materials that are resistant to wear, corrosion, and fatigue—such as certain alloys, ceramics, and polymers—are ideal for parts subject to small oscillatory movements. Additionally, surface coatings such as anti-corrosion treatments or wear-resistant coatings can help protect against fretting wear and fretting corrosion.
- Surface Coatings: Specialized coatings, such as DLC (Diamond-Like Carbon) or hard anodizing, can reduce friction and wear between mating surfaces, preventing fretting wear. These coatings also provide an additional layer of protection against corrosion.
2. Design Modifications
Improper component design is often a contributor to fretting. Design modifications to minimize relative motion between mating surfaces can significantly reduce fretting risk. For example:
- Improving Fit and Tolerances: Tightening the tolerance and ensuring a precise fit between mating components can reduce the movement between them, thereby reducing fretting.
- Eliminating Unnecessary Vibration: Minimizing unnecessary vibrations in a system through better design or dampers can also help reduce the impact of fretting.
3. Surface Treatments
Several surface treatments can help reduce the risk of fretting in automotive systems. For example:
- Hardening and Shot Peening: These processes introduce compressive stresses to the surface of metal components, which helps them resist the micro-movements that cause fretting.
- Lubrication: In some cases, lubricants can reduce friction between mating surfaces and minimize wear and corrosion caused by fretting. For example, molybdenum disulfide or graphite-based lubricants are often used in high-contact areas like bearings and suspension joints.
4. Regular Inspection and Maintenance
Routine maintenance and inspection are essential for identifying early signs of fretting damage and addressing it before it worsens. Regularly checking electrical connectors for corrosion, inspecting bearings for wear, and replacing components that show signs of fretting can help maintain optimal vehicle performance.
5. Environmental Control
Fretting corrosion is often exacerbated by environmental conditions such as moisture and contaminants. Ensuring that automotive components are sealed and protected from exposure to harsh elements can reduce the chances of fretting corrosion.
6. Vibration Isolation
Vibration isolation techniques, such as rubber bushings, vibration dampers, and isolators, can help mitigate the small oscillations that contribute to fretting damage. In automotive applications, these techniques are often used in areas like suspension, drivetrain, and electrical connectors to reduce the frequency and amplitude of micro-movements.
Conclusion:
Fretting is a pervasive issue in automotive systems that can lead to wear, corrosion, and eventual component failure. While it is often overlooked, its impact on vehicle reliability and performance can be significant.
Understanding the causes and manifestations of fretting and implementing preventive measures like proper material selection, surface coatings, design modifications, and regular maintenance can go a long way in extending the lifespan of automotive components.
By addressing fretting early and employing effective mitigation strategies, automotive manufacturers and vehicle owners can ensure that their vehicles operate smoothly and safely for years